What is the Common Production Process for Capacitors?
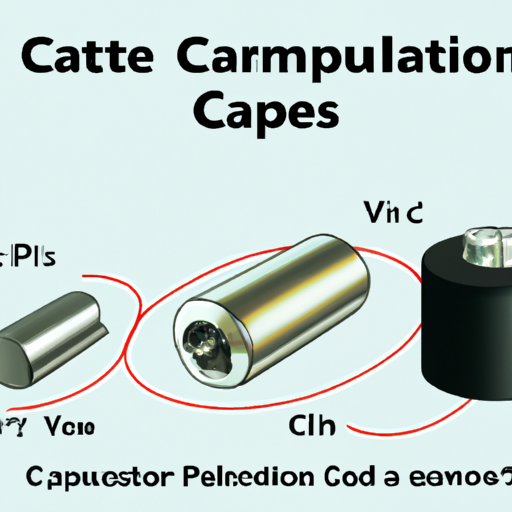
I. Introduction
Capacitors are essential components in electronic devices, serving as energy storage units that can release energy quickly when needed. They play a crucial role in various applications, from smoothing out voltage fluctuations in power supplies to enabling signal processing in communication devices. Understanding the production process of capacitors is vital for appreciating their functionality and the technological advancements that continue to shape their development.
II. Types of Capacitors
Capacitors come in various types, each designed for specific applications and performance characteristics.
A. Ceramic Capacitors
Ceramic capacitors are widely used due to their small size and reliability. They are made from ceramic materials that serve as the dielectric, providing excellent stability and low losses.
B. Electrolytic Capacitors
Electrolytic capacitors are polarized devices that offer high capacitance values in a compact form. They are commonly used in power supply circuits and audio applications.
C. Film Capacitors
Film capacitors utilize thin plastic films as dielectrics. They are known for their stability and low self-inductance, making them suitable for high-frequency applications.
D. Tantalum Capacitors
Tantalum capacitors are known for their high capacitance-to-volume ratio and reliability. They are often used in military and aerospace applications due to their robustness.
E. Supercapacitors
Supercapacitors, or ultracapacitors, provide high energy density and rapid charge/discharge capabilities. They are increasingly used in energy storage systems and hybrid vehicles.
F. Comparison of Different Types
Each type of capacitor has its advantages and disadvantages, making them suitable for different applications. For instance, while ceramic capacitors are excellent for high-frequency applications, electrolytic capacitors are preferred for bulk energy storage.
III. Raw Materials
A. Overview of Materials Used in Capacitor Production
The production of capacitors involves various raw materials, primarily dielectric and conductive materials.
1. Dielectric Materials
Dielectric materials are crucial for capacitor function, as they store electrical energy. Common dielectric materials include ceramic, plastic films, and electrolytic solutions.
2. Conductive Materials
Conductive materials, such as aluminum and tantalum, are used for the electrodes. The choice of material affects the capacitor's performance, including its capacitance and voltage rating.
B. Sourcing and Quality Control of Raw Materials
Sourcing high-quality raw materials is essential for ensuring the reliability and performance of capacitors. Manufacturers often implement stringent quality control measures to verify the purity and consistency of materials used in production.
IV. Production Process
The production process of capacitors involves several key steps, from design and engineering to manufacturing and quality control.
A. Design and Engineering
1. Specifications and Requirements
The first step in capacitor production is defining the specifications based on the intended application. This includes determining capacitance values, voltage ratings, and physical dimensions.
2. Prototyping and Testing
Once specifications are established, prototypes are created and tested to ensure they meet performance criteria. This phase is critical for identifying potential issues before mass production.
B. Manufacturing Steps
1. Dielectric Layer Preparation
The dielectric layer is a fundamental component of capacitors.
a. Material Selection
The choice of dielectric material is based on the desired electrical properties and application requirements.
b. Layer Thickness and Uniformity
Manufacturers must ensure that the dielectric layer is of uniform thickness to maintain consistent performance across all capacitors produced.
2. Electrode Preparation
Electrodes are prepared using conductive materials.
a. Material Selection
The selection of electrode material, such as aluminum for electrolytic capacitors or tantalum for tantalum capacitors, is crucial for performance.
b. Coating and Deposition Techniques
Electrodes are often coated or deposited using techniques like sputtering or chemical vapor deposition to achieve the desired properties.
3. Assembly of Capacitor Components
The assembly process involves stacking the dielectric and electrode layers.
a. Layer Stacking
Layers are carefully stacked to ensure proper alignment and contact between the dielectric and electrodes.
b. Connection of Electrodes
Electrodes are connected to external terminals, allowing the capacitor to be integrated into electronic circuits.
4. Encapsulation and Packaging
Once assembled, capacitors are encapsulated to protect them from environmental factors.
a. Protective Coatings
Protective coatings are applied to enhance durability and prevent moisture ingress.
b. Form Factor Considerations
The final packaging must consider the intended application, ensuring that the capacitor fits within the design constraints of the electronic device.
C. Quality Control and Testing
Quality control is a critical aspect of capacitor production, ensuring that each component meets stringent performance standards.
1. Electrical Testing
Capacitors undergo electrical testing to verify capacitance, voltage rating, and leakage current.
2. Mechanical Testing
Mechanical tests assess the physical integrity of capacitors, including resistance to vibration and thermal cycling.
3. Reliability Testing
Reliability testing simulates long-term usage conditions to ensure that capacitors will perform consistently over their expected lifespan.
V. Environmental Considerations
A. Sustainable Practices in Capacitor Production
As environmental concerns grow, manufacturers are adopting sustainable practices in capacitor production. This includes using eco-friendly materials and reducing energy consumption during manufacturing.
B. Waste Management and Recycling
Effective waste management strategies are implemented to minimize the environmental impact of capacitor production. Additionally, recycling programs are established to recover valuable materials from end-of-life capacitors.
C. Compliance with Environmental Regulations
Manufacturers must comply with various environmental regulations, ensuring that their production processes do not harm the environment or public health.
VI. Innovations in Capacitor Production
A. Advances in Materials Science
Recent advancements in materials science have led to the development of new dielectric and conductive materials, enhancing capacitor performance and expanding their applications.
B. Automation and Industry 4.0
The integration of automation and Industry 4.0 technologies in capacitor production has improved efficiency and precision, allowing for higher production rates and reduced costs.
C. Future Trends in Capacitor Technology
Future trends in capacitor technology include the development of smaller, more efficient capacitors with higher energy densities, driven by the demand for compact electronic devices and renewable energy solutions.
VII. Conclusion
The production process for capacitors is a complex and multifaceted endeavor that requires careful consideration of materials, design, and manufacturing techniques. As technology continues to evolve, so too will the methods used to produce capacitors, ensuring that they remain integral components in the ever-advancing world of electronics. Continuous improvement and innovation in capacitor production will play a vital role in meeting the demands of future technologies, from consumer electronics to renewable energy systems.
VIII. References
- Academic journals on materials science and electrical engineering.
- Industry reports on capacitor technology and market trends.
- Manufacturer guidelines and specifications for various types of capacitors.
This comprehensive overview of the common production process for capacitors highlights the intricate steps involved in creating these essential electronic components. By understanding this process, we can better appreciate the role capacitors play in modern technology and the ongoing innovations that will shape their future.
What is the Common Production Process for Capacitors?
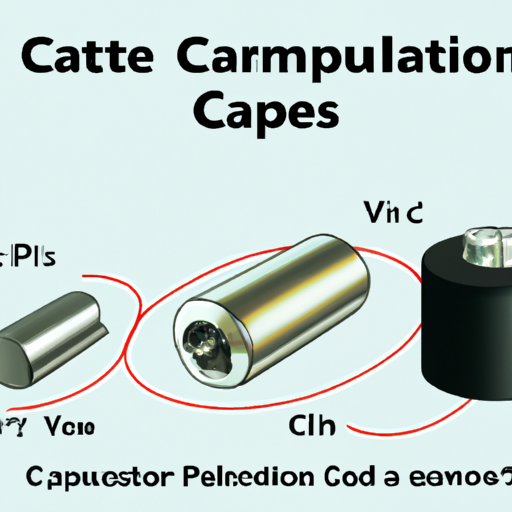
I. Introduction
Capacitors are essential components in electronic devices, serving as energy storage units that can release energy quickly when needed. They play a crucial role in various applications, from smoothing out voltage fluctuations in power supplies to enabling signal processing in communication devices. Understanding the production process of capacitors is vital for appreciating their functionality and the technological advancements that continue to shape their development.
II. Types of Capacitors
Capacitors come in various types, each designed for specific applications and performance characteristics.
A. Ceramic Capacitors
Ceramic capacitors are widely used due to their small size and reliability. They are made from ceramic materials that serve as the dielectric, providing excellent stability and low losses.
B. Electrolytic Capacitors
Electrolytic capacitors are polarized devices that offer high capacitance values in a compact form. They are commonly used in power supply circuits and audio applications.
C. Film Capacitors
Film capacitors utilize thin plastic films as dielectrics. They are known for their stability and low self-inductance, making them suitable for high-frequency applications.
D. Tantalum Capacitors
Tantalum capacitors are known for their high capacitance-to-volume ratio and reliability. They are often used in military and aerospace applications due to their robustness.
E. Supercapacitors
Supercapacitors, or ultracapacitors, provide high energy density and rapid charge/discharge capabilities. They are increasingly used in energy storage systems and hybrid vehicles.
F. Comparison of Different Types
Each type of capacitor has its advantages and disadvantages, making them suitable for different applications. For instance, while ceramic capacitors are excellent for high-frequency applications, electrolytic capacitors are preferred for bulk energy storage.
III. Raw Materials
A. Overview of Materials Used in Capacitor Production
The production of capacitors involves various raw materials, primarily dielectric and conductive materials.
1. Dielectric Materials
Dielectric materials are crucial for capacitor function, as they store electrical energy. Common dielectric materials include ceramic, plastic films, and electrolytic solutions.
2. Conductive Materials
Conductive materials, such as aluminum and tantalum, are used for the electrodes. The choice of material affects the capacitor's performance, including its capacitance and voltage rating.
B. Sourcing and Quality Control of Raw Materials
Sourcing high-quality raw materials is essential for ensuring the reliability and performance of capacitors. Manufacturers often implement stringent quality control measures to verify the purity and consistency of materials used in production.
IV. Production Process
The production process of capacitors involves several key steps, from design and engineering to manufacturing and quality control.
A. Design and Engineering
1. Specifications and Requirements
The first step in capacitor production is defining the specifications based on the intended application. This includes determining capacitance values, voltage ratings, and physical dimensions.
2. Prototyping and Testing
Once specifications are established, prototypes are created and tested to ensure they meet performance criteria. This phase is critical for identifying potential issues before mass production.
B. Manufacturing Steps
1. Dielectric Layer Preparation
The dielectric layer is a fundamental component of capacitors.
a. Material Selection
The choice of dielectric material is based on the desired electrical properties and application requirements.
b. Layer Thickness and Uniformity
Manufacturers must ensure that the dielectric layer is of uniform thickness to maintain consistent performance across all capacitors produced.
2. Electrode Preparation
Electrodes are prepared using conductive materials.
a. Material Selection
The selection of electrode material, such as aluminum for electrolytic capacitors or tantalum for tantalum capacitors, is crucial for performance.
b. Coating and Deposition Techniques
Electrodes are often coated or deposited using techniques like sputtering or chemical vapor deposition to achieve the desired properties.
3. Assembly of Capacitor Components
The assembly process involves stacking the dielectric and electrode layers.
a. Layer Stacking
Layers are carefully stacked to ensure proper alignment and contact between the dielectric and electrodes.
b. Connection of Electrodes
Electrodes are connected to external terminals, allowing the capacitor to be integrated into electronic circuits.
4. Encapsulation and Packaging
Once assembled, capacitors are encapsulated to protect them from environmental factors.
a. Protective Coatings
Protective coatings are applied to enhance durability and prevent moisture ingress.
b. Form Factor Considerations
The final packaging must consider the intended application, ensuring that the capacitor fits within the design constraints of the electronic device.
C. Quality Control and Testing
Quality control is a critical aspect of capacitor production, ensuring that each component meets stringent performance standards.
1. Electrical Testing
Capacitors undergo electrical testing to verify capacitance, voltage rating, and leakage current.
2. Mechanical Testing
Mechanical tests assess the physical integrity of capacitors, including resistance to vibration and thermal cycling.
3. Reliability Testing
Reliability testing simulates long-term usage conditions to ensure that capacitors will perform consistently over their expected lifespan.
V. Environmental Considerations
A. Sustainable Practices in Capacitor Production
As environmental concerns grow, manufacturers are adopting sustainable practices in capacitor production. This includes using eco-friendly materials and reducing energy consumption during manufacturing.
B. Waste Management and Recycling
Effective waste management strategies are implemented to minimize the environmental impact of capacitor production. Additionally, recycling programs are established to recover valuable materials from end-of-life capacitors.
C. Compliance with Environmental Regulations
Manufacturers must comply with various environmental regulations, ensuring that their production processes do not harm the environment or public health.
VI. Innovations in Capacitor Production
A. Advances in Materials Science
Recent advancements in materials science have led to the development of new dielectric and conductive materials, enhancing capacitor performance and expanding their applications.
B. Automation and Industry 4.0
The integration of automation and Industry 4.0 technologies in capacitor production has improved efficiency and precision, allowing for higher production rates and reduced costs.
C. Future Trends in Capacitor Technology
Future trends in capacitor technology include the development of smaller, more efficient capacitors with higher energy densities, driven by the demand for compact electronic devices and renewable energy solutions.
VII. Conclusion
The production process for capacitors is a complex and multifaceted endeavor that requires careful consideration of materials, design, and manufacturing techniques. As technology continues to evolve, so too will the methods used to produce capacitors, ensuring that they remain integral components in the ever-advancing world of electronics. Continuous improvement and innovation in capacitor production will play a vital role in meeting the demands of future technologies, from consumer electronics to renewable energy systems.
VIII. References
- Academic journals on materials science and electrical engineering.
- Industry reports on capacitor technology and market trends.
- Manufacturer guidelines and specifications for various types of capacitors.
This comprehensive overview of the common production process for capacitors highlights the intricate steps involved in creating these essential electronic components. By understanding this process, we can better appreciate the role capacitors play in modern technology and the ongoing innovations that will shape their future.