Common Production Processes for Cable Assembly Testers
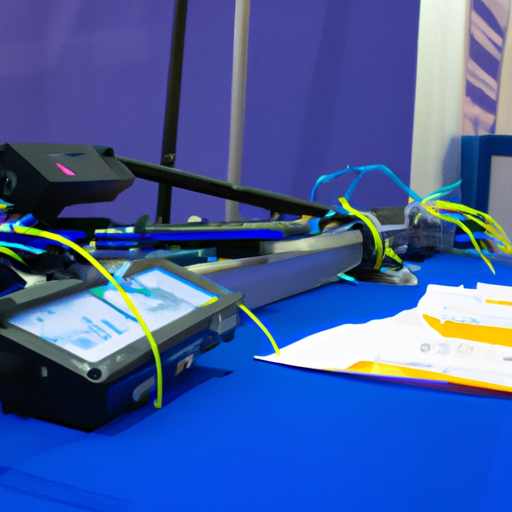
I. Introduction
In the world of electronics, the reliability and performance of cable assemblies are paramount. Cable assembly testers play a crucial role in ensuring that these assemblies function correctly and meet industry standards. These testers are designed to evaluate the integrity and performance of cable assemblies, which are essential components in various electronic devices. This blog post will explore the common production processes involved in creating cable assembly testers, highlighting the importance of each step in delivering high-quality testing solutions.
II. Understanding Cable Assembly Testers
A. Types of Cable Assembly Testers
Cable assembly testers can be categorized into three main types: manual testers, automated testers, and hybrid testers.
1. **Manual Testers**: These testers require human intervention to operate. They are often used for simple testing tasks and are cost-effective for small-scale operations.
2. **Automated Testers**: These systems are designed for high-volume testing and can perform multiple tests simultaneously without human intervention. They are equipped with advanced software and hardware to ensure accuracy and efficiency.
3. **Hybrid Testers**: Combining elements of both manual and automated testers, hybrid testers offer flexibility and can be used in various testing scenarios.
B. Key Features and Functions
Cable assembly testers are equipped with several key features that enhance their functionality:
1. **Signal Integrity Testing**: This feature ensures that the signals transmitted through the cable assemblies maintain their integrity, which is crucial for high-speed data transmission.
2. **Continuity Testing**: This function checks for any breaks or faults in the cable assembly, ensuring that all connections are intact.
3. **Performance Testing**: This involves assessing the overall performance of the cable assembly under various conditions to ensure it meets specified standards.
III. Overview of Production Processes
The production of cable assembly testers involves several critical processes, each contributing to the final product's quality and reliability.
A. Design and Prototyping
1. **Initial Design Considerations**: The design phase begins with understanding the requirements of the tester, including the types of cables it will test and the specific functionalities needed.
2. **Prototyping Techniques**: Once the design is established, prototypes are created using various techniques, such as 3D printing or PCB design software, to visualize and test the concept.
3. **Testing Prototypes for Functionality**: Prototypes undergo rigorous testing to ensure they meet design specifications and function as intended. This phase is crucial for identifying any design flaws early in the process.
B. Material Selection
1. **Types of Materials Used**: The materials selected for the production of cable assembly testers include high-quality plastics, metals, and electronic components that can withstand the rigors of testing.
2. **Supplier Selection and Quality Assurance**: Choosing reliable suppliers is essential for ensuring that the materials meet quality standards. Quality assurance processes are implemented to verify the integrity of the materials before they are used in production.
C. Manufacturing Processes
1. **PCB Fabrication**:
- **Design Files and Gerber Data**: The design files, including Gerber data, are prepared for PCB fabrication, detailing the layout and specifications of the circuit board.
- **Etching and Layering**: The PCB is fabricated through processes such as etching and layering, where copper is removed to create the desired circuit patterns.
2. **Component Sourcing and Assembly**:
- **Sourcing Components**: Components such as resistors, capacitors, and connectors are sourced from trusted suppliers to ensure compatibility and reliability.
- **Assembly Techniques**: Various assembly techniques, including soldering and surface mount technology (SMT), are employed to attach components to the PCB.
3. **Enclosure Manufacturing**:
- **Design and Material Choices**: The enclosure design is crucial for protecting the internal components. Materials are selected based on durability and aesthetic considerations.
- **Assembly of Enclosures**: The final assembly involves fitting the PCB and components into the enclosure, ensuring that all parts are securely housed.
D. Calibration and Testing
1. **Calibration Procedures**: Calibration is essential to ensure that the tester provides accurate readings. This involves adjusting the tester's settings based on known standards.
2. **Functional Testing**: After calibration, the tester undergoes functional testing to verify that it operates correctly and meets performance specifications.
3. **Quality Control Measures**: Quality control measures are implemented throughout the production process to identify and rectify any issues before the final product is released.
IV. Quality Assurance in Production
A. Importance of Quality Assurance
Quality assurance is critical in the production of cable assembly testers, as it ensures that the final product meets industry standards and customer expectations. A robust quality assurance process minimizes defects and enhances the reliability of the testers.
B. Common Quality Assurance Practices
1. **In-Process Inspections**: Regular inspections during the manufacturing process help identify potential issues early, allowing for timely corrections.
2. **Final Product Testing**: Before the testers are shipped, they undergo comprehensive testing to ensure they function correctly and meet all specifications.
3. **Compliance with Industry Standards**: Adhering to industry standards, such as ISO and IPC, is essential for maintaining quality and ensuring that the products are safe and reliable.
C. Documentation and Traceability
Maintaining thorough documentation throughout the production process is vital for traceability. This includes records of materials used, testing results, and any changes made during production. Such documentation is essential for quality audits and future reference.
V. Challenges in Production Processes
A. Common Challenges Faced
1. **Component Availability**: Fluctuations in the availability of electronic components can disrupt production schedules and lead to delays.
2. **Technological Changes**: Rapid advancements in technology can render certain components or processes obsolete, necessitating continuous updates to production methods.
3. **Cost Management**: Balancing quality with cost-effectiveness is a constant challenge in the production of cable assembly testers.
B. Strategies to Overcome Challenges
1. **Supplier Relationships**: Building strong relationships with suppliers can help ensure a steady supply of components and mitigate the impact of shortages.
2. **Lean Manufacturing Techniques**: Implementing lean manufacturing principles can enhance efficiency and reduce waste, ultimately lowering production costs.
3. **Continuous Improvement Practices**: Adopting a culture of continuous improvement encourages teams to identify and implement enhancements in the production process.
VI. Future Trends in Cable Assembly Testing Production
A. Advancements in Technology
1. **Automation and Robotics**: The integration of automation and robotics in production processes is expected to increase efficiency and reduce human error, leading to higher quality products.
2. **Smart Testing Solutions**: The development of smart testing solutions, which utilize artificial intelligence and machine learning, will enhance the capabilities of cable assembly testers, allowing for more sophisticated testing methods.
B. Sustainability in Production
1. **Eco-Friendly Materials**: There is a growing trend towards using eco-friendly materials in the production of cable assembly testers, aligning with global sustainability goals.
2. **Waste Reduction Strategies**: Implementing waste reduction strategies in manufacturing processes can minimize environmental impact and improve overall efficiency.
VII. Conclusion
In conclusion, the production processes for cable assembly testers are multifaceted and require careful planning and execution. From design and prototyping to quality assurance and future trends, each step plays a vital role in delivering reliable and effective testing solutions. As technology continues to advance, the industry must adapt to new challenges and opportunities, ensuring that cable assembly testers remain essential tools in the electronics sector.
VIII. References
- Industry Publications
- Technical Standards and Guidelines
- Relevant Case Studies and Research Papers
This comprehensive overview of the production processes for cable assembly testers highlights the importance of each phase in ensuring the quality and reliability of these critical testing tools. By understanding these processes, manufacturers can better navigate the challenges of production and embrace future trends that will shape the industry.
Common Production Processes for Cable Assembly Testers
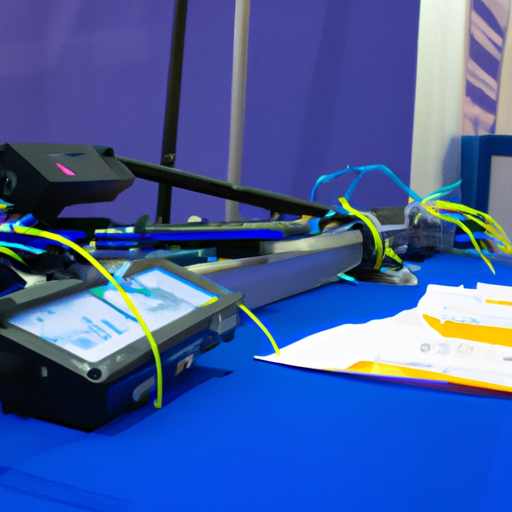
I. Introduction
In the world of electronics, the reliability and performance of cable assemblies are paramount. Cable assembly testers play a crucial role in ensuring that these assemblies function correctly and meet industry standards. These testers are designed to evaluate the integrity and performance of cable assemblies, which are essential components in various electronic devices. This blog post will explore the common production processes involved in creating cable assembly testers, highlighting the importance of each step in delivering high-quality testing solutions.
II. Understanding Cable Assembly Testers
A. Types of Cable Assembly Testers
Cable assembly testers can be categorized into three main types: manual testers, automated testers, and hybrid testers.
1. **Manual Testers**: These testers require human intervention to operate. They are often used for simple testing tasks and are cost-effective for small-scale operations.
2. **Automated Testers**: These systems are designed for high-volume testing and can perform multiple tests simultaneously without human intervention. They are equipped with advanced software and hardware to ensure accuracy and efficiency.
3. **Hybrid Testers**: Combining elements of both manual and automated testers, hybrid testers offer flexibility and can be used in various testing scenarios.
B. Key Features and Functions
Cable assembly testers are equipped with several key features that enhance their functionality:
1. **Signal Integrity Testing**: This feature ensures that the signals transmitted through the cable assemblies maintain their integrity, which is crucial for high-speed data transmission.
2. **Continuity Testing**: This function checks for any breaks or faults in the cable assembly, ensuring that all connections are intact.
3. **Performance Testing**: This involves assessing the overall performance of the cable assembly under various conditions to ensure it meets specified standards.
III. Overview of Production Processes
The production of cable assembly testers involves several critical processes, each contributing to the final product's quality and reliability.
A. Design and Prototyping
1. **Initial Design Considerations**: The design phase begins with understanding the requirements of the tester, including the types of cables it will test and the specific functionalities needed.
2. **Prototyping Techniques**: Once the design is established, prototypes are created using various techniques, such as 3D printing or PCB design software, to visualize and test the concept.
3. **Testing Prototypes for Functionality**: Prototypes undergo rigorous testing to ensure they meet design specifications and function as intended. This phase is crucial for identifying any design flaws early in the process.
B. Material Selection
1. **Types of Materials Used**: The materials selected for the production of cable assembly testers include high-quality plastics, metals, and electronic components that can withstand the rigors of testing.
2. **Supplier Selection and Quality Assurance**: Choosing reliable suppliers is essential for ensuring that the materials meet quality standards. Quality assurance processes are implemented to verify the integrity of the materials before they are used in production.
C. Manufacturing Processes
1. **PCB Fabrication**:
- **Design Files and Gerber Data**: The design files, including Gerber data, are prepared for PCB fabrication, detailing the layout and specifications of the circuit board.
- **Etching and Layering**: The PCB is fabricated through processes such as etching and layering, where copper is removed to create the desired circuit patterns.
2. **Component Sourcing and Assembly**:
- **Sourcing Components**: Components such as resistors, capacitors, and connectors are sourced from trusted suppliers to ensure compatibility and reliability.
- **Assembly Techniques**: Various assembly techniques, including soldering and surface mount technology (SMT), are employed to attach components to the PCB.
3. **Enclosure Manufacturing**:
- **Design and Material Choices**: The enclosure design is crucial for protecting the internal components. Materials are selected based on durability and aesthetic considerations.
- **Assembly of Enclosures**: The final assembly involves fitting the PCB and components into the enclosure, ensuring that all parts are securely housed.
D. Calibration and Testing
1. **Calibration Procedures**: Calibration is essential to ensure that the tester provides accurate readings. This involves adjusting the tester's settings based on known standards.
2. **Functional Testing**: After calibration, the tester undergoes functional testing to verify that it operates correctly and meets performance specifications.
3. **Quality Control Measures**: Quality control measures are implemented throughout the production process to identify and rectify any issues before the final product is released.
IV. Quality Assurance in Production
A. Importance of Quality Assurance
Quality assurance is critical in the production of cable assembly testers, as it ensures that the final product meets industry standards and customer expectations. A robust quality assurance process minimizes defects and enhances the reliability of the testers.
B. Common Quality Assurance Practices
1. **In-Process Inspections**: Regular inspections during the manufacturing process help identify potential issues early, allowing for timely corrections.
2. **Final Product Testing**: Before the testers are shipped, they undergo comprehensive testing to ensure they function correctly and meet all specifications.
3. **Compliance with Industry Standards**: Adhering to industry standards, such as ISO and IPC, is essential for maintaining quality and ensuring that the products are safe and reliable.
C. Documentation and Traceability
Maintaining thorough documentation throughout the production process is vital for traceability. This includes records of materials used, testing results, and any changes made during production. Such documentation is essential for quality audits and future reference.
V. Challenges in Production Processes
A. Common Challenges Faced
1. **Component Availability**: Fluctuations in the availability of electronic components can disrupt production schedules and lead to delays.
2. **Technological Changes**: Rapid advancements in technology can render certain components or processes obsolete, necessitating continuous updates to production methods.
3. **Cost Management**: Balancing quality with cost-effectiveness is a constant challenge in the production of cable assembly testers.
B. Strategies to Overcome Challenges
1. **Supplier Relationships**: Building strong relationships with suppliers can help ensure a steady supply of components and mitigate the impact of shortages.
2. **Lean Manufacturing Techniques**: Implementing lean manufacturing principles can enhance efficiency and reduce waste, ultimately lowering production costs.
3. **Continuous Improvement Practices**: Adopting a culture of continuous improvement encourages teams to identify and implement enhancements in the production process.
VI. Future Trends in Cable Assembly Testing Production
A. Advancements in Technology
1. **Automation and Robotics**: The integration of automation and robotics in production processes is expected to increase efficiency and reduce human error, leading to higher quality products.
2. **Smart Testing Solutions**: The development of smart testing solutions, which utilize artificial intelligence and machine learning, will enhance the capabilities of cable assembly testers, allowing for more sophisticated testing methods.
B. Sustainability in Production
1. **Eco-Friendly Materials**: There is a growing trend towards using eco-friendly materials in the production of cable assembly testers, aligning with global sustainability goals.
2. **Waste Reduction Strategies**: Implementing waste reduction strategies in manufacturing processes can minimize environmental impact and improve overall efficiency.
VII. Conclusion
In conclusion, the production processes for cable assembly testers are multifaceted and require careful planning and execution. From design and prototyping to quality assurance and future trends, each step plays a vital role in delivering reliable and effective testing solutions. As technology continues to advance, the industry must adapt to new challenges and opportunities, ensuring that cable assembly testers remain essential tools in the electronics sector.
VIII. References
- Industry Publications
- Technical Standards and Guidelines
- Relevant Case Studies and Research Papers
This comprehensive overview of the production processes for cable assembly testers highlights the importance of each phase in ensuring the quality and reliability of these critical testing tools. By understanding these processes, manufacturers can better navigate the challenges of production and embrace future trends that will shape the industry.