The Difference Between Cable Assembly and Cable Assembly
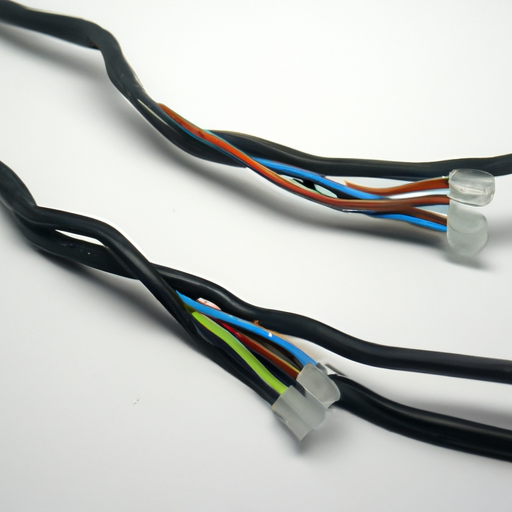
I. Introduction
In the world of electronics and electrical engineering, the term "cable assembly" is frequently used, yet it can often lead to confusion. While it may seem straightforward, understanding the nuances of cable assembly is crucial for professionals and enthusiasts alike. This article aims to clarify what cable assembly entails, explore its various types and applications, and highlight the differences between standard and custom cable assemblies.
II. What is Cable Assembly?
A. Definition and Components
Cable assembly refers to the process of assembling various components, including wires, connectors, and insulation, into a single functional unit. The primary components of a cable assembly include:
1. **Wires and Cables**: These are the conductive elements that carry electrical signals or power. They can vary in size, material, and insulation type, depending on the application.
2. **Connectors and Terminals**: These components facilitate the connection of the cable assembly to other devices or systems. They come in various shapes and sizes, designed for specific applications.
3. **Insulation and Sheathing**: Insulation protects the conductive elements from environmental factors and prevents short circuits. Sheathing provides additional protection and can also enhance the cable's durability.
B. Types of Cable Assemblies
Cable assemblies can be broadly categorized into two types:
1. **Custom Cable Assemblies**: These are tailored to meet specific requirements of a project or application. They are designed based on unique specifications, such as length, connector type, and environmental conditions.
2. **Standard Cable Assemblies**: These are pre-manufactured assemblies that adhere to common specifications and are readily available for general use. They are often used in applications where customization is not critical.
C. Applications of Cable Assemblies
Cable assemblies find applications across various industries, including:
1. **Industrial**: Used in machinery, automation systems, and control panels.
2. **Automotive**: Essential for wiring harnesses, sensors, and electronic control units.
3. **Telecommunications**: Critical for data transmission and connectivity in networks.
4. **Consumer Electronics**: Found in devices such as computers, televisions, and smartphones.
III. The Process of Cable Assembly
A. Design and Engineering
The cable assembly process begins with design and engineering, which involves:
1. **Requirements Gathering**: Understanding the specific needs of the application, including electrical specifications and environmental factors.
2. **Prototyping**: Creating initial prototypes to test the design and functionality before full-scale production.
B. Manufacturing
Once the design is finalized, the manufacturing process begins, which includes:
1. **Material Selection**: Choosing the right materials for wires, connectors, and insulation based on performance requirements.
2. **Assembly Techniques**: Various techniques are employed to assemble the components, including:
- **Crimping**: A method of joining two pieces of metal by deforming one or both to hold them together.
- **Soldering**: A process of joining electrical components using a filler metal that melts at a low temperature.
- **Overmolding**: A technique where a layer of material is molded over the assembly to provide additional protection.
C. Quality Control
Quality control is a critical aspect of cable assembly, involving:
1. **Testing Procedures**: Rigorous testing to ensure the assembly meets electrical and mechanical specifications.
2. **Compliance Standards**: Adhering to industry standards and regulations to ensure safety and reliability.
IV. The Concept of Cable Assembly in Different Contexts
A. Cable Assembly in General Use
In general use, cable assembly refers to the standard practices and components involved in creating functional electrical connections. However, misconceptions often arise regarding the complexity and customization involved in the process.
B. Cable Assembly in Specialized Applications
In specialized applications, cable assemblies can be highly complex and tailored for specific environments, such as:
1. **High-Performance Cable Assemblies**: Designed for applications requiring superior performance, such as high-speed data transmission.
2. **Military and Aerospace Applications**: These assemblies must meet stringent standards for durability and reliability in extreme conditions.
3. **Medical Device Cable Assemblies**: Require compliance with strict regulations to ensure safety and effectiveness in medical applications.
V. The Importance of Customization in Cable Assembly
A. Benefits of Custom Cable Assemblies
Custom cable assemblies offer several advantages:
1. **Tailored Solutions**: They are designed to meet the specific needs of a project, ensuring optimal performance.
2. **Enhanced Performance**: Custom assemblies can improve efficiency and reliability in critical applications.
B. Factors Influencing Customization
Several factors influence the need for customization, including:
1. **Environmental Considerations**: Factors such as temperature, humidity, and exposure to chemicals can dictate the materials and design of the assembly.
2. **Specific Industry Requirements**: Different industries have unique standards and regulations that must be adhered to.
VI. Comparing Cable Assembly with Cable Assembly
A. Similarities
Despite the differences, standard and custom cable assemblies share several similarities:
1. **Basic Components**: Both types consist of wires, connectors, and insulation.
2. **Manufacturing Processes**: The fundamental processes of design, assembly, and quality control are similar.
B. Differences
The key differences between standard and custom cable assemblies include:
1. **Application Scope**: Standard assemblies are used in general applications, while custom assemblies are tailored for specific needs.
2. **Customization Levels**: Custom assemblies offer a higher degree of customization in terms of design and materials.
3. **Performance Specifications**: Custom assemblies often have stricter performance specifications to meet unique requirements.
VII. Case Studies
A. Example of Standard Cable Assembly
A standard cable assembly might be used in a consumer electronic device, such as a smartphone charger. This assembly typically includes a USB connector, a standard wire gauge, and basic insulation. Its design is optimized for mass production, ensuring cost-effectiveness and reliability.
B. Example of Custom Cable Assembly
In contrast, a custom cable assembly might be used in a medical device, such as a heart monitor. This assembly would require specific materials that meet medical standards, unique connector types, and insulation designed to withstand sterilization processes. The customization ensures that the device operates safely and effectively in a critical environment.
C. Analysis of Performance and Outcomes
The performance of standard cable assemblies is generally reliable for everyday applications, while custom assemblies can significantly enhance the functionality and safety of specialized devices. The investment in custom solutions often pays off in terms of performance and compliance with industry standards.
VIII. Future Trends in Cable Assembly
A. Technological Advancements
The future of cable assembly is being shaped by technological advancements, including:
1. **Automation in Manufacturing**: Increased automation is streamlining the assembly process, improving efficiency and reducing costs.
2. **Smart Cable Assemblies**: The integration of smart technology into cable assemblies is enabling real-time monitoring and diagnostics.
B. Sustainability Considerations
As industries move towards sustainability, cable assembly manufacturers are focusing on:
1. **Eco-Friendly Materials**: The use of recyclable and biodegradable materials is becoming more prevalent.
2. **Recycling and Waste Management**: Implementing recycling programs to minimize waste and promote sustainability in production processes.
IX. Conclusion
In summary, understanding the differences between standard and custom cable assemblies is essential for making informed decisions in various applications. While both types share fundamental components and manufacturing processes, their applications, levels of customization, and performance specifications can vary significantly. As technology continues to evolve, the future of cable assembly promises exciting advancements that will enhance performance and sustainability.
X. References
A comprehensive list of relevant literature and sources can be found in the references section, providing additional resources for further reading on cable assembly and its applications.
The Difference Between Cable Assembly and Cable Assembly
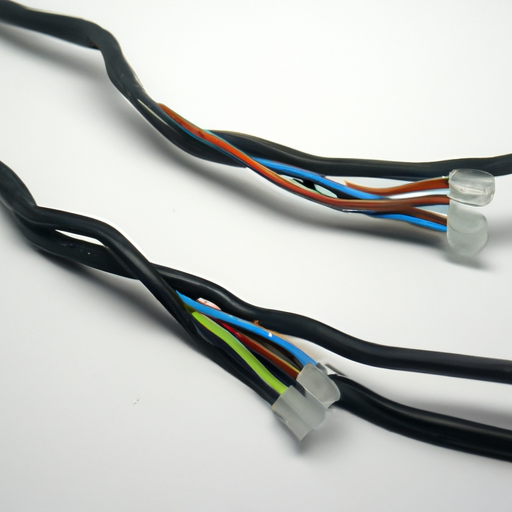
I. Introduction
In the world of electronics and electrical engineering, the term "cable assembly" is frequently used, yet it can often lead to confusion. While it may seem straightforward, understanding the nuances of cable assembly is crucial for professionals and enthusiasts alike. This article aims to clarify what cable assembly entails, explore its various types and applications, and highlight the differences between standard and custom cable assemblies.
II. What is Cable Assembly?
A. Definition and Components
Cable assembly refers to the process of assembling various components, including wires, connectors, and insulation, into a single functional unit. The primary components of a cable assembly include:
1. **Wires and Cables**: These are the conductive elements that carry electrical signals or power. They can vary in size, material, and insulation type, depending on the application.
2. **Connectors and Terminals**: These components facilitate the connection of the cable assembly to other devices or systems. They come in various shapes and sizes, designed for specific applications.
3. **Insulation and Sheathing**: Insulation protects the conductive elements from environmental factors and prevents short circuits. Sheathing provides additional protection and can also enhance the cable's durability.
B. Types of Cable Assemblies
Cable assemblies can be broadly categorized into two types:
1. **Custom Cable Assemblies**: These are tailored to meet specific requirements of a project or application. They are designed based on unique specifications, such as length, connector type, and environmental conditions.
2. **Standard Cable Assemblies**: These are pre-manufactured assemblies that adhere to common specifications and are readily available for general use. They are often used in applications where customization is not critical.
C. Applications of Cable Assemblies
Cable assemblies find applications across various industries, including:
1. **Industrial**: Used in machinery, automation systems, and control panels.
2. **Automotive**: Essential for wiring harnesses, sensors, and electronic control units.
3. **Telecommunications**: Critical for data transmission and connectivity in networks.
4. **Consumer Electronics**: Found in devices such as computers, televisions, and smartphones.
III. The Process of Cable Assembly
A. Design and Engineering
The cable assembly process begins with design and engineering, which involves:
1. **Requirements Gathering**: Understanding the specific needs of the application, including electrical specifications and environmental factors.
2. **Prototyping**: Creating initial prototypes to test the design and functionality before full-scale production.
B. Manufacturing
Once the design is finalized, the manufacturing process begins, which includes:
1. **Material Selection**: Choosing the right materials for wires, connectors, and insulation based on performance requirements.
2. **Assembly Techniques**: Various techniques are employed to assemble the components, including:
- **Crimping**: A method of joining two pieces of metal by deforming one or both to hold them together.
- **Soldering**: A process of joining electrical components using a filler metal that melts at a low temperature.
- **Overmolding**: A technique where a layer of material is molded over the assembly to provide additional protection.
C. Quality Control
Quality control is a critical aspect of cable assembly, involving:
1. **Testing Procedures**: Rigorous testing to ensure the assembly meets electrical and mechanical specifications.
2. **Compliance Standards**: Adhering to industry standards and regulations to ensure safety and reliability.
IV. The Concept of Cable Assembly in Different Contexts
A. Cable Assembly in General Use
In general use, cable assembly refers to the standard practices and components involved in creating functional electrical connections. However, misconceptions often arise regarding the complexity and customization involved in the process.
B. Cable Assembly in Specialized Applications
In specialized applications, cable assemblies can be highly complex and tailored for specific environments, such as:
1. **High-Performance Cable Assemblies**: Designed for applications requiring superior performance, such as high-speed data transmission.
2. **Military and Aerospace Applications**: These assemblies must meet stringent standards for durability and reliability in extreme conditions.
3. **Medical Device Cable Assemblies**: Require compliance with strict regulations to ensure safety and effectiveness in medical applications.
V. The Importance of Customization in Cable Assembly
A. Benefits of Custom Cable Assemblies
Custom cable assemblies offer several advantages:
1. **Tailored Solutions**: They are designed to meet the specific needs of a project, ensuring optimal performance.
2. **Enhanced Performance**: Custom assemblies can improve efficiency and reliability in critical applications.
B. Factors Influencing Customization
Several factors influence the need for customization, including:
1. **Environmental Considerations**: Factors such as temperature, humidity, and exposure to chemicals can dictate the materials and design of the assembly.
2. **Specific Industry Requirements**: Different industries have unique standards and regulations that must be adhered to.
VI. Comparing Cable Assembly with Cable Assembly
A. Similarities
Despite the differences, standard and custom cable assemblies share several similarities:
1. **Basic Components**: Both types consist of wires, connectors, and insulation.
2. **Manufacturing Processes**: The fundamental processes of design, assembly, and quality control are similar.
B. Differences
The key differences between standard and custom cable assemblies include:
1. **Application Scope**: Standard assemblies are used in general applications, while custom assemblies are tailored for specific needs.
2. **Customization Levels**: Custom assemblies offer a higher degree of customization in terms of design and materials.
3. **Performance Specifications**: Custom assemblies often have stricter performance specifications to meet unique requirements.
VII. Case Studies
A. Example of Standard Cable Assembly
A standard cable assembly might be used in a consumer electronic device, such as a smartphone charger. This assembly typically includes a USB connector, a standard wire gauge, and basic insulation. Its design is optimized for mass production, ensuring cost-effectiveness and reliability.
B. Example of Custom Cable Assembly
In contrast, a custom cable assembly might be used in a medical device, such as a heart monitor. This assembly would require specific materials that meet medical standards, unique connector types, and insulation designed to withstand sterilization processes. The customization ensures that the device operates safely and effectively in a critical environment.
C. Analysis of Performance and Outcomes
The performance of standard cable assemblies is generally reliable for everyday applications, while custom assemblies can significantly enhance the functionality and safety of specialized devices. The investment in custom solutions often pays off in terms of performance and compliance with industry standards.
VIII. Future Trends in Cable Assembly
A. Technological Advancements
The future of cable assembly is being shaped by technological advancements, including:
1. **Automation in Manufacturing**: Increased automation is streamlining the assembly process, improving efficiency and reducing costs.
2. **Smart Cable Assemblies**: The integration of smart technology into cable assemblies is enabling real-time monitoring and diagnostics.
B. Sustainability Considerations
As industries move towards sustainability, cable assembly manufacturers are focusing on:
1. **Eco-Friendly Materials**: The use of recyclable and biodegradable materials is becoming more prevalent.
2. **Recycling and Waste Management**: Implementing recycling programs to minimize waste and promote sustainability in production processes.
IX. Conclusion
In summary, understanding the differences between standard and custom cable assemblies is essential for making informed decisions in various applications. While both types share fundamental components and manufacturing processes, their applications, levels of customization, and performance specifications can vary significantly. As technology continues to evolve, the future of cable assembly promises exciting advancements that will enhance performance and sustainability.
X. References
A comprehensive list of relevant literature and sources can be found in the references section, providing additional resources for further reading on cable assembly and its applications.